Introduction: The Intricate Science of Glassmaking
Glassmaking is a remarkable material that has captivated humanity for millennia. As an amorphous solid, glass is created through a series of intricate chemical reactions and carefully controlled processes. In this article, we will explore the science behind glass manufacturing, examining each stage of production and the chemical transformations that turn raw materials into the transparent, durable glass we use in countless applications.
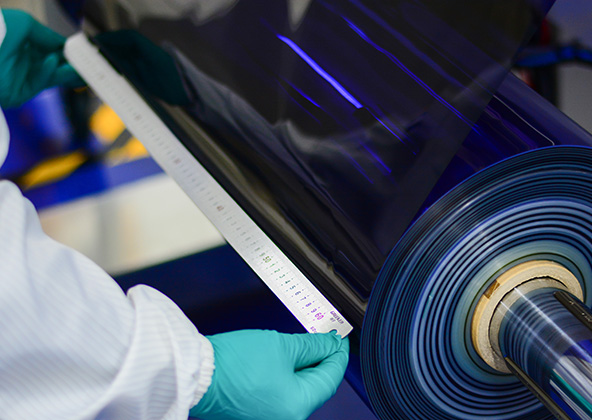
Raw Materials: The Foundation of Glass Production
The production of glass begins with the careful selection of raw materials. The primary ingredient in glass manufacturing is silica, or silicon dioxide, which is typically sourced from sand. In addition to silica, other crucial ingredients include soda ash (sodium carbonate) and limestone (calcium carbonate). These materials are combined in precise proportions to create the glass batch, which will undergo significant transformations during the manufacturing process.
The Melting Process: Chemical Reactions in the Furnace
Once the raw materials are combined, the batch is heated in a furnace to extremely high temperatures, usually around 1700 degrees Celsius (3000 degrees Fahrenheit). At this stage, a series of vital chemical reactions occurs. The soda ash decomposes into sodium oxide and carbon dioxide, while the limestone breaks down into calcium oxide and carbon dioxide. These reactions are essential in lowering the melting point of the silica and achieving the correct viscosity, allowing the molten mixture to be shaped into glass.
Forming the Glass: Shaping the Molten Substance
After the batch has melted and the chemical reactions are complete, the molten glass is ready to be formed. Various methods can be used to shape the glass, including blowing, pressing, and pulling. For example, in the process of blown glass, a blob of molten glass is gathered onto a blowpipe and then inflated. The glassblower carefully shapes the glass by manipulating it with tools and adjusting the air pressure inside the blowpipe. Each technique allows for the creation of different glass products, from intricate artworks to everyday items.
Annealing: Cooling and Solidifying the Glass
Once the glass has been formed into its final shape, it must undergo annealing. This process involves slowly cooling the glass in a controlled environment. Annealing is a critical step, as it helps to relieve internal stresses within the glass, preventing cracking and ensuring the product’s durability. Proper annealing enhances the overall quality of the glass, making it suitable for a wide range of uses.
Conclusion: The Complex and Captivating World of Glassmaking
The production of glass is a complex and scientifically rich process, involving a sequence of chemical reactions and precise techniques. From the selection of raw materials to the final annealing, each step plays an essential role in transforming raw silica into the beautiful, functional glass products we rely on every day. Glass manufacturing, with its blend of ancient craftsmanship and modern science, continues to be a fascinating field of study and innovation.
Summary FAQ: The Science Behind Glassmaking
Q: What are the primary raw materials used in glass production?
A: The primary raw materials are silica (silicon dioxide), soda ash (sodium carbonate), and limestone (calcium carbonate).
Q: What happens during the melting process in glass production?
A: During the melting process, the raw materials are heated in a furnace, where soda ash and limestone decompose into oxides, lowering the melting point of silica and creating a molten mixture ready for shaping.
Q: How is glass shaped after it is melted?
A: Glass can be shaped using various techniques such as blowing, pressing, or pulling. These methods allow the molten glass to be formed into different products.
Q: What is the purpose of annealing in glass manufacturing?
A: Annealing involves slowly cooling the glass in a controlled environment to relieve internal stresses, preventing cracking and ensuring the final product’s quality and durability.